In this article
Importance of SolidWorks in the Manufacturing Industry
What is the use of SolidWorks in manufacturing?
Understanding the Role of CAD in Manufacturing
Specific Features of SolidWorks that Benefit Manufacturing
Key Uses of SolidWorks in Manufacturing
What are the Benefits of Using SolidWorks in Manufacturing
Real-world Examples of SolidWorks in Manufacturing
SolidWorks in Medical Device Manufacturing
SolidWorks in Energy Sector Manufacturing
How SolidWorks Helps to Meet Industry Standards
FAQs
In today’s cutthroat global market, the ability to design and develop products rapidly, precisely, and efficiently is more important than ever. That’s where SolidWorks manufacturing comes into play. By providing a unified platform for the creation of 3D models, advanced simulations, and detailed documentation, this CAD software has become the standard for the manufacturing industry.
The use of SolidWorks in manufacturing has grown exponentially over the years, solidifying its place as an essential tool in modern production processes. Proficiency in SolidWorks skills to match industry standards has become a key competency sought by employers in the industry, encouraging professionals and students alike to turn to resources like Wiingy for comprehensive SolidWorks tutorials and training.
Struggling with 3D Modelling? Try a free lesson of our Online Solidworks Tutoring and Learn from Architects and Designers proficient in CAD Softwares.
Importance of SolidWorks in the Manufacturing Industry
SolidWorks manufacturing is at the center of the modern manufacturing industry, where it plays a crucial role in hastening product development, enhancing collaboration, and stimulating innovation. With SolidWorks, you can have everything you need to design, prototype, and manufacture a product in one place.
According to recent research from the Boston Consulting Group, companies that utilize advanced CAD tools like SolidWorks can reduce product development costs by up to 15%, and shorten the product development time by up to 20%.
What is the use of SolidWorks in manufacturing?
SolidWorks is not just a design tool; it is a comprehensive solution for manufacturing challenges. It facilitates product design, simulation, cost estimation, and technical documentation creation. In the context of SolidWorks manufacturing, it becomes an unified platform for managing complex processes from initial design to final production.
Understanding the Role of CAD in Manufacturing
In the realm of manufacturing, CAD tools have revolutionized the way products are designed and produced. SolidWorks, as a top-tier CAD software, enables manufacturers to visualize and analyze their designs under real-world conditions, significantly reducing the need for physical prototypes. For instance, in 2022, Airbus reported a 30% reduction in prototype costs after adopting SolidWorks as its primary CAD tool.
Specific Features of SolidWorks that Benefit Manufacturing
SolidWorks offers a multitude of specialized features that streamline and optimize the manufacturing process. From intuitive design tools to advanced simulation capabilities, these features are tailored to address the unique needs and challenges faced by manufacturers.
- Parametric Modelling: Enables engineers to create models based on a set of mathematical equations, resulting in more accurate designs.
- Design Automation: Simplifies repetitive design tasks, increasing productivity, and reducing the likelihood of errors.
- Advanced Simulation: Provides the ability to test designs under real-world conditions, reducing the need for costly physical prototypes.
- Cost Estimation: Offers real-time cost estimation tools, aiding in better decision-making and budget planning.
Key Uses of SolidWorks in Manufacturing
SolidWorks plays a critical role in many aspects of the manufacturing process. Its diverse capabilities and applications make it a versatile tool that manufacturers can leverage to enhance efficiency, accuracy, and collaboration throughout the product development cycle.
A. Design and Prototyping
Using SolidWorks for product design is a straightforward, efficient process. The software’s intuitive interface and comprehensive toolset enable designers to bring their visions to life with precision and speed. SolidWorks’ parametric design capabilities allow for quick modifications, ensuring designs can be easily adjusted in response to changing requirements. According to a survey by Tech-Clarity, companies using SolidWorks for design reported a 15% increase in design productivity.
Rapid prototyping with SolidWorks has revolutionized the manufacturing process. By enabling designers to create accurate 3D models and conduct simulations, SolidWorks reduces the need for physical prototypes, saving time and resources. This can result in significant cost savings; the Aberdeen Group reported that companies implementing rapid prototyping strategies could reduce prototyping costs by up to 60%.
B. Manufacturing Process Planning
SolidWorks’ role in manufacturing process planning cannot be overstated. Its advanced assembly tools and integrated design-to-manufacturing system streamline the process of turning 3D designs into physical products. By automating routine tasks and allowing for easy revisions, SolidWorks helps manufacturers ensure that their processes are efficient, flexible, and cost-effective.
C. Quality Assurance and Control
SolidWorks helps manufacturers uphold high standards of quality. Its simulation tools allow for extensive testing of designs under realistic conditions, enabling potential issues to be identified and addressed before production. Furthermore, SolidWorks’ model-based definition (MBD) capabilities provide comprehensive 3D annotations, ensuring everyone involved in the manufacturing process has the information they need to maintain quality standards.
D. Production Cost Estimation
Using SolidWorks for cost estimation can have a significant impact on a manufacturer’s bottom line. The software’s cost estimation tools provide real-time feedback on manufacturing costs as designs are created and modified. This allows manufacturers to make informed decisions about materials, manufacturing methods, and design modifications to control costs. According to a survey by Tech-Clarity, companies using automated cost estimation tools like those in SolidWorks were able to reduce their product costs by an average of 12%.
What are the Benefits of Using SolidWorks in Manufacturing
Implementing SolidWorks in manufacturing offers a wide array of advantages. Beyond its technical prowess in design and simulation, SolidWorks can greatly enhance workflow efficiency, foster improved collaboration, and contribute to cost-effective management throughout the product lifecycle.
- Increased design efficiency: SolidWorks’ advanced tools and automated features enable designers to create high-quality models more quickly and accurately.
- Improved communication and collaboration: SolidWorks’ collaborative tools and extensive compatibility with other systems allow for smoother workflows and better communication among team members and departments.
- Enhanced production accuracy: SolidWorks’ simulation and testing capabilities ensure designs are thoroughly vetted before production, reducing the risk of costly mistakes.
- Cost-effective product lifecycle management: SolidWorks’ integrated design-to-manufacturing system and cost estimation tools ensure efficient, cost-effective production processes.
Real-world Examples of SolidWorks in Manufacturing
The power and utility of SolidWorks become most evident when looking at its application in real-world manufacturing scenarios. Across diverse industries, from automotive and aerospace to consumer goods and medical devices, SolidWorks has been instrumental in driving innovation and productivity.
Case study: SolidWorks in automotive manufacturing
Toyota, a leading automotive manufacturer, uses SolidWorks to streamline its design and manufacturing processes. Using SolidWorks, Toyota managed to decrease their design time by 30% while improving the quality and safety of their vehicles.
Case study: SolidWorks in aerospace manufacturing
SpaceX, the pioneering private aerospace manufacturer, uses SolidWorks for designing its groundbreaking space exploration vehicles. By utilizing SolidWorks, SpaceX was able to reduce the design-to-manufacture time for their Falcon 1 vehicle by 30%.
Case study: SolidWorks in consumer goods manufacturing
Dyson, a global technology company known for its innovative consumer goods, uses SolidWorks in the development of its products. Through SolidWorks manufacturing, Dyson managed to reduce its product development cycle by 20%, allowing for faster time to market.
SolidWorks in Medical Device Manufacturing
Medical device manufacturers are challenged to deliver products that are not only innovative and reliable but also compliant with strict industry standards. SolidWorks can play a crucial role here, providing comprehensive capabilities for design, simulation, data management, and communication in one unified platform.
Case study: SolidWorks in Medical Device Manufacturing
Boston Scientific, a leading medical device manufacturer, reported a 20% reduction in their design cycles after implementing SolidWorks. By using SolidWorks for product design and testing, they could meet rigorous quality standards while accelerating time-to-market.
SolidWorks in Energy Sector Manufacturing
In the energy sector, companies face unique challenges in designing and manufacturing components for oil, gas, solar, and wind energy systems. SolidWorks manufacturing capabilities can provide an integrated environment for the design of complex parts, assemblies, and systems, simulation of operational conditions, and development of manufacturing documentation.
Case study: SolidWorks in Energy Sector Manufacturing
Vestas Wind Systems, a Danish manufacturer of wind turbines, reported that SolidWorks helped them increase their product development efficiency by 20%. Their designers used SolidWorks’ powerful simulation tools to analyze and optimize designs under real-world conditions, reducing the need for costly and time-consuming physical prototypes.
How SolidWorks Helps to Meet Industry Standards
Maintaining compliance with industry standards is critical in the manufacturing sector. SolidWorks provides comprehensive tools for validating design compliance and creating the necessary documentation. It also includes features to automate the generation of reports and technical drawings that adhere to industry-standard formats.
The use of SolidWorks in manufacturing is paving the way for increased efficiency, cost reductions, improved quality, and better communication within the sector. As this article has shown, manufacturers from various industries – from automotive and aerospace to consumer goods, medical devices, and energy – leverage SolidWorks to enhance their design and production processes. Learning and mastering SolidWorks skills to match industry standards is becoming an essential move for aspiring professionals in this industry.
Platforms like wiingy are helping to bridge the knowledge gap by offering comprehensive tutorials and training sessions on SolidWorks. As the manufacturing landscape continues to evolve, so too will the role of SolidWorks, reinforcing its position as an integral tool in modern manufacturing.
Struggling with 3D Modelling? Try a free lesson of our Online Solidworks Tutoring and Learn from Architects and Designers proficient in CAD Softwares.
FAQs
What big companies use SolidWorks?
SolidWorks is used by a number of well-known businesses across a wide range of industries. Tesla, Samsung, NASA, Boeing, Google, Apple, Boston Scientific, Toyota, and others are among these industry leaders.
What are the best uses for SolidWorks?
In addition to its traditional uses in product design and simulation, SolidWorks is also utilized in the planning of manufacturing processes, quality control, cost estimation, and more. The software’s robust features make it a flexible resource that can be put to use in a variety of manufacturing and other settings.
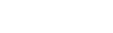
Mar 06, 2025
Was this helpful?