An Insight into SOLIDWORKS Simulation: Finite Element Analysis (FEA) Software
By Shefali Sundram on Aug 02, 2023
Updated Jan 29, 2025

In this article
In the world of engineering and design, SolidWorks Simulation plays an integral role in validating product performance.
As part of the SOLIDWORKS suite, Simulation is a Finite Element Analysis (FEA) software tool that allows engineers to virtually test how their designs will respond to real-world forces, vibrations, heat, and other physical effects.
This reduces the need for physical prototypes, leading to lower costs and faster time to market.
Struggling with 3D Modelling? Try a free lesson of our Online Solidworks Tutoring and Learn from Architects and Designers proficient in CAD Softwares.
What Is Simulation in SOLIDWORKS?
SOLIDWORKS Simulation is a powerful, easy-to-use design analysis tool that’s fully integrated within the SOLIDWORKS platform. It uses the method of Finite Element Analysis (FEA) to predict a product’s real-world physical behavior by virtually testing CAD models. This software enables engineers to precisely define the environment in which it will operate and solve complex physics problems such as nonlinear elasticity, dynamics, plasticity, and heat transfer.
Importance & Applications of SOLIDWORKS Simulation in Engineering and Design
In modern product design and development, Simulation is not just a “nice-to-have” but a critical part of the process. Its importance lies in the ability to:
- Evaluate Designs Early: Design flaws can be detected early in the design process, reducing the need for costly modifications and reworks later on.
- Optimize Products: Engineers can explore various design scenarios and select the optimal one that meets their performance criteria.
- Reduce Prototyping Costs: With virtual testing, the need for expensive and time-consuming physical prototypes is significantly reduced.
- Improve Product Quality: By testing designs under real-world conditions, products are more reliable and have higher quality.
Applications of SOLIDWORKS Simulation span across various industries including automotive, aerospace, consumer products, heavy machinery, and medical devices, to name a few.
How accurate are the results?
Accuracy in SOLIDWORKS Simulation is heavily dependent on the user’s expertise in setting up the simulation, understanding the limitations of the software, and interpreting the results correctly. With the correct setup, Simulation can deliver highly accurate results. However, it’s important to validate these results with physical testing whenever possible to ensure maximum reliability and accuracy.
The SOLIDWORKS Simulation suite is a comprehensive tool with a range of features catering to various industry needs. Let’s delve into some of its key features in the next section.
What are the Features of SolidWorks Simulation?
SolidWorks Simulation offers a comprehensive set of features that cater to a variety of engineering and design needs. Let’s explore them one by one.
Linear Static Analysis for Parts and Assemblies
This is the most basic form of FEA and is used for evaluating the strength of a part or assembly under loading conditions. It assumes the relationship between the loads and deformation to be linear. For example, it can be used to check the strength of a bridge under specific load conditions.
Time-based Motion Analysis
This feature is used to evaluate the movement and forces within a mechanical assembly over a period of time. For instance, this can be used in designing machinery parts to ensure optimal performance and lifespan.
Frequency Analysis
This is used to determine the natural frequencies and mode shapes of a structure. It’s useful in reducing noise, preventing resonance, and improving the stability of a product. For example, it can be used to test the vibration of an engine part in a car.
Buckling Analysis
Buckling analysis predicts the buckling strength (or critical load) of a structure. It’s crucial in fields such as aerospace or civil engineering where failure due to buckling can have catastrophic effects. For instance, it can be used to analyze the stability of a tall building under wind loads.
Thermal Analysis
This feature evaluates a design’s response to heat and cooling effects. It’s beneficial in sectors where temperature changes significantly impact product performance, such as electronics or automotive design. For example, it can simulate the heat dispersion in a computer chip under operation.
Optimization Analysis
Optimization analysis helps in exploring all possible iterations of a design solution under defined conditions. This is to identify the best design that meets the performance criteria and constraints. For instance, it can be used to optimize the weight and strength of an aircraft wing.
Non-Linear Analysis
Non-linear analysis is used when the response of a structure to loads is not linear, such as large deformations, plastic behavior, and material nonlinearity. An example use case can be the deformation analysis of a rubber seal.
Drop Test Analysis
This feature simulates the impact force when a product is dropped from a certain height, helping designers to enhance the durability of the product. It can be used, for example, in the design of mobile phones to improve their resistance to drops.
Fatigue Analysis
Fatigue analysis is used to estimate the life of a product when subjected to cyclic loading and unloading over time. It can be used, for example, to predict the life expectancy of a car’s suspension system.
Pressure Vessel Design
This feature is used for the design and analysis of pressure vessels, ensuring they meet the necessary safety standards. It is crucial in industries such as oil and gas, power generation, and chemical processing.
Submodeling Simulations
Submodeling is a technique where a detailed analysis is performed on a particular region of a larger assembly. This is often used when you want to focus your analysis on a small section of a large assembly without needing to analyze the entire model.
This variety of features makes SOLIDWORKS Simulation a comprehensive tool for addressing the diverse needs of industries. In the following section, we’ll delve into various simulation packages that SOLIDWORKS offers.
Simulation Packages
To cater to different design analysis needs, SOLIDWORKS offers various simulation packages. Each package has specialized features to handle different types of analysis. Below is a quick overview:
- SOLIDWORKS Simulation Standard: This package provides an entry-level simulation solution. It includes features for linear static analysis for parts and assemblies, time-based motion simulation, and fatigue analysis. It’s perfect for companies just stepping into simulation space.
- SOLIDWORKS Simulation Professional: The professional package offers all the features of the standard package, and additional tools like frequency analysis, thermal analysis, drop test analysis, buckling analysis, and pressure vessel design. It also includes 2D simplification and submodeling. This package is well-suited for companies that need more advanced simulation capabilities.
- SOLIDWORKS Simulation Premium: This is the top-tier package. It includes all features from the lower tiers and additional advanced features such as nonlinear and dynamic analysis. It’s designed for companies that require sophisticated analysis like large deformation, advanced material models, or dynamic response.
By offering a range of packages, SOLIDWORKS Simulation provides flexibility, enabling users to choose the one that best fits their specific needs. Whether you’re a small business just starting with simulation or a larger company with more complex needs, there’s a package for you.
Understanding Simulation Results
When using SolidWorks Simulation, it is important to know how to interpret and understand the results. This includes understanding stress distribution, deformation, displacement, and factor of safety, among others. The program offers visual outputs such as graphs and animations, as well as numerical outputs in tabular form. These results can help determine if your design will survive its intended environment and usage.
Validation of Simulation Results
It’s equally essential to validate your simulation results. While SolidWorks Simulation is a powerful tool, it’s always necessary to compare simulation results with real-world data to ensure accuracy. Conducting physical tests on prototypes and comparing those results with simulations can help confirm the fidelity of the software’s predictions.
Simulation Best Practices
Successful simulation using SolidWorks Simulation depends on following best practices. These include:
- Understanding your problem: Define the purpose of your simulation. Are you looking to determine stress distribution, deformation, or fluid flow? Understanding what you are trying to solve will help guide the simulation process.
- Selecting the appropriate study type: Choose the correct study type for your problem. For example, use linear static studies for low-stress, small-deformation problems, and use dynamic studies for problems involving significant time-dependent forces.
- Properly applying fixtures and loads: Incorrectly applied fixtures and loads can yield inaccurate results. Make sure to accurately apply these to your model.
- Refining the mesh: Mesh size can significantly affect your results. A finer mesh can yield more accurate results but requires more computational resources.
- Interpreting the results: Understand what the results are showing and what they mean for your design.
By following these best practices, engineers and designers can effectively use SolidWorks Simulation to analyze and improve their designs.
The SolidWorks Simulation software is an advanced FEA tool, offering features that cover a broad range of analysis types. Whether you are analyzing the structural stability of a building, the heat dispersion of a computer chip, or the vibration of an engine part, SolidWorks Simulation provides the tools you need to simulate and analyze your design accurately.
By investing time to learn SolidWorks online and understand how to utilize these tools, engineers and designers can ensure their designs will perform as intended in the real world, reducing the time and cost associated with physical prototyping and testing.
Now that we’ve explored the depths of SolidWorks Simulation, you should be equipped with a solid understanding of its capabilities. From linear static analysis to complex non-linear dynamics, it serves as an indispensable tool in the modern engineering and design toolbox. With SolidWorks Simulation, the possibilities are truly endless.
Struggling with 3D Modelling? Try a free lesson of our Online Solidworks Tutoring and Learn from Architects and Designers proficient in CAD Softwares.
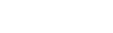
Jan 29, 2025
Was this helpful?